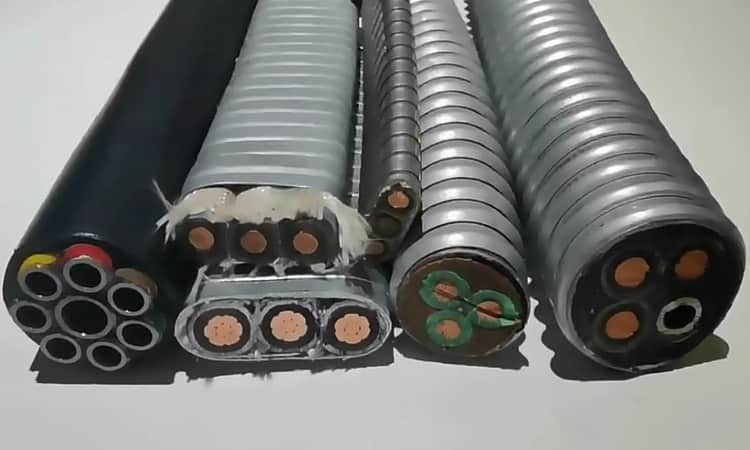
ESP Cable
ESP Power Cable
ESP cable are specifically designed for use in electric submersible pump (ESP) systems, where they function as the lifeline that connects the power source to the submerged pump motor. These cables are subjected to harsh environmental conditions, including prolonged submersion in water, exposure to corrosive chemicals, and high temperatures. Therefore, their design and construction must be meticulous to ensure reliability, durability, and safety.
ESP Cable Structure Materials
1. Conductor: Single-strand tinned copper wire, adhering to GOST 22483-2012 Class 1 standards, ensuring optimal electrical conductivity.
2.Insulation: High-dielectric ethylene propylene diene monomer (EPDM) rubber, providing robust insulation capable of withstanding downhole temperatures reaching 450°F (232°C).
3. Lead Sheath: Encasing the conductors, this lead sheath offers superior protection against gases and aggressive fluids.
Mechanical Strength Enhancement: Synthetic tape wrapping reinforces the assembly, boosting overall mechanical strength and durability.
4.Armor Layer Options:
Galvanized Steel: Suitable for basic corrosion resistance requirements.
Corrosion-Resistant Steel: Offers enhanced protection for more demanding environments.
MONEL Alloy: Ultra-corrosion-resistant, ideal for the harshest conditions, including extreme pressures.
Chemical Injection System: A stainless steel capillary tube integrated for the injection of scale and corrosion inhibitors, maintaining the integrity of the cable over extended periods.
5.EPDM Insulation Characteristics
High Dielectric Strength: The ethylene propylene copolymer (EPDM) insulation boasts exceptional dielectric properties, allowing for dependable performance even in downhole temperatures soaring to 450°F (232°C), ensuring uninterrupted operation in challenging subsurface environments.
Three-Core ESP cable
Type | Rated voltage | Nominal cross-section and number of cores | Compliance with American Wire Gauge | Tinned core diameter | Core diameter on insulation | Size with armor | Length per reel |
KESBP-230-4 | 4 kV | 0.0124 sq in. (8.00 mm2) x 3 pcs | 0.126 in. | 0.241 in. | 0.473×1.168 in. | 35500 ft | |
0,0130 sq in. (8.37 mm) x 3 pcs | AWG8 | 0.129 in. | 0.244 in. | 0.475×1.176 in. | 35000 ft | ||
0.0155 sq in. (10.00 mm2) x 3 pcs | 0.141 in. | 0.256 in. | 0.488×1.213 in. | 33000 ft | |||
0.0163 sq in. (10.5 mm2) x 3 pcs | AWG7 | 0.144 in. | 0.260 in. | 0.492×1.223 in. | 32000 ft | ||
0.0206 sq in. (13.3 mm2) x 3 pcs | AWG6 | 0.162 in. | 0.278 in. | 0.510×1.278 in. | 29000 ft | ||
0.0248 sq in. (16.0 mm2) x 3 pcs | 0.178 in. | 0.293 in. | 0.525×1.324 in. | 27000 ft | |||
0.0260 sq in. (16.8 mm2) x 3 pcs | AWG5 | 0182 in. | 0.298 in. | 0,530×1,337 in. | 26500 ft | ||
0,0329 sq in. (21,20 mm2) x 3 pcs | AWG4 | 0.205 in. | 0.320 in. | 0.551×1.406 in. | 23500 ft | ||
0.0388 sq in. (25.00 mm2) x 3 pcs | 0.222 in. | 0.344 in. | 0.576×1.476 in. | 21000 ft | |||
0.0414 sq in. (26.7 mm2) x 3 pcs | AWG3 | 0.230 in. | 0.352 in. | 0.583×1.499 in. | 20500 ft | ||
0.0521 sq in. (33.6 mm2) x 3 pcs | AWG2 | 0.258 in. | 0.380 in. | 0.611×1.582 in. | 18000 ft | ||
0.0543 sq in. (35.0 mm2) x 3 pcs | 0.263 in. | 0.385 in. | 0.617×1.599 in. | 18000 ft | |||
0.0651 sq in. (42.0 mm2) x 3 pcs | 0.288 in. | 0.410 in. | 0,641×1,674 in. | 16000 ft | |||
0.0657 sq in. (42.4 mm2) x 3 pcs | AWG1 | 0.290 in. | 0.411 in. | 0.643×1.678 in. | 16000 ft | ||
0.0775 sq in. (50.0 mm2) x 3 pcs | 0.314 in. (7.984 mm) | 0.436 in. | 0,668×1,753 in. | 14500 ft | |||
0.0830 sq in. (53.5 mm2) x 3 pcs | AWG0 | 0.325 in. | 0.447 in. | 0.679×1.785 in. | 14000 ft | ||
KESBP-230-5 | 5 kV | 0.0124 sq in. (8.00 mm2) x 3 pcs | 0.126 in. (3.194 mm) | 0.267 in. | 0.515×1.293 in. | 28000 ft | |
0.0130 sq in. (8.37 mm2) x 3 pcs | AWG8 | 0.129 in. | 0.270 in. | 0.517×1.302 in. | 27500 ft | ||
0.0155 sq in. (10.00 mm) x 3 pcs | 0.141 in. | 0.282 in. | 0.530х1.338 in. | 26000 ft | |||
0.0163 sq in. (10.5 mm2) x 3 pcs | AWG7 | 0.144 in. | 0.286 in. | 0.533×1.349 in. | 25500 ft | ||
0,0206 sq in. (13.3 mm2) x 3 pcs | AWG6 | 0.162 in. | 0 .304 in. | 0.552×1.403 in. | 23000 ft | ||
0.0248 sq in. 16.0×3 | 0.178 in. | 0.319 in. | 0.570×1.449 in. | 21500 ft | |||
0.0260 sq in. (16.8 mm2) x 3 pcs | AWG5 | 0.182 in. | 0.323 in. | 0.571×1.462 in. | 21000 ft | ||
0.0329 sq in. (21.20 mm2) x 3 pcs | AWG4 | 0.205 in. | 0.346 in. | 0.594×1.531 in. | 19000 ft | ||
0.0388 sq in. (25.00 mm2) x 3 pcs | 0.222 in. | 0.364 in. | 0.611×1.582 in. | 17500 ft | |||
0.0414 sq in. (26.7 mm2) x 3 pcs | AWG3 | 0.230 in. | 0.371 in. | 0,619х1,605 in. | 17000 ft | ||
0.0521 sq in. (33.6 mm2) x 3 pcs | AWG2 | 0.258 in. | 0.399 in. | 0.647×1.689 in. | 15000 ft | ||
0.0543 sq in. (35.0 mm2) x 3 pcs | 0.263 | 0.405 in. | 0.652×0.651 in. | 15000 ft | |||
0.0651 sq in. (42.0 mm2) x 3 pcs | 0.288 in. | 0.430 in. | 0.677×1.790 in | 13500 ft | |||
0,0657 sq in. (42.4 mm2) x 3 pcs | AWG1 | 0.290 in. | 0.431 in. | 0,679×1,785 in. | 13500 ft | ||
0.0775 sq in. (50.0 mm2) x 3 pcs | 0.314 in. | 0.456 in. | 0.704×1.859 in. | 12000 ft | |||
0,0830 sq in. (53.5 mm2) x 3 pcs | AWG0 | 0.325 in. | 0.467 in. | 0,714×1,89 in. | 12000 ft |
Three-core ESP cable with ⅜-in. chemical injection capillary tube
Type | Rated voltage | Nominal cross-section and number of cores | Compliance with American Wire Gauge | Tinned core diameter | Core diameter on insulation | Capillary pipe diameter | Size with armor | Length per reel |
KASBP-230-4-1 | 4 kV | 0,0260 sq in. (16.8 mm) x 3 pcs | AWG5 | 0.182 in. (4.624 mm) | 0.298 in. | ⅜» (9.5 mm) | 0.530×1.712 in. | 16000 ft (5000 m) |
0.0329 sq in. (21.2 mm) x 3 pcs | AWG4 | 0.205 in. (5.204 mm) | 0.320 in. | 0.552×1.781 in. (14.03х45.23 mm) | 14500 ft | |||
0.0521 sq in. (33.6 mm) x 3 pcs | AWG2 | 0.257 in. (6.544 mm) | 0.380 in. | 0.611×1.958 in. (15.53х49.73 mm) | 12000 ft | |||
0.0657 sq in. (42.4 mm2) x 3 pcs | AWG1 | 0.290 in. (7.354 mm) | 0.411 in. | 0.643×2.054 in. (16.34х52.16 mm) | 11000 ft | |||
0,0775 sq in. (50.0 mm2) x 3 pcs | 0.314 in. (7.984 mm) | 0,436 in. | 0,668×2,128 in. (16.97х54.05 mm) | 10000 ft | ||||
0.0830 sq in. (53.5 mm2) x 3 pcs | AWG0 | 0.325 in. (8.254 mm) | 0.447 in. | 0.679×2.16 in. (17.24х54.86 mm) | 9500 ft | |||
KASBP-230-4-1
| 5 kV | 0.0260 sq in. (16.8 mm2 x 3 pcs) | AWG5 | 0.182 in. (4.624 mm) | 0.324 in. | 0.571×1.837 in. (14.51х46.67 mm) | 16000 ft | |
0.0329 sq in. (21.2 mm2) x 3 pcs | AWG4 | 0.205 in. (5,204 mm) | 0.346 in. | 0.594×1.906 in. (15.09х48.41 mm) | 14500 ft | |||
0.0521 sq in. (33.6 mm2) x 3 pcs | AWG2 | 0.258 in. (6.544 mm) | 0.399 in. | 0.647×2,06 in. (16.43х52.43 mm) | 12000 ft | |||
0,0657 sq in. (42.4 mm2) x 3 pcs | AWG1 | 0.290 in. (7.354 mm) | 0,431 in. | 0.679×2.160 in. (17.24х54.86 mm) | 11000 ft | |||
0.0775 sq in. (50.0 mm2) x 3 pcs | 0.314 in. (7.984 mm) | 0.456 in. | 0.704×2.234 in. (17.87х56.75 mm) | 10000 ft | ||||
0,0829 sq in, (53.5 mm2) x 3 pcs | AWG0 | 0.325 in. (8.254 mm) | 0,467 in. | 0.714×2.266 in. (18.14х57.56 mm) | 9500 ft |
Applications of ESP Cable
ESP (Electric Submersible Pump) Cable is a specialized type of cable designed for use in oil and gas wells, particularly in deepwater or challenging subsurface environments. Its unique construction and material composition make it suitable for a variety of critical applications within the oil and gas industry.
Deepwater Oil & Gas Production: ESP cables are essential in deepwater drilling and production operations, where they enable the electric submersible pump to be powered from the surface. The cable transmits electrical energy to the pump, located thousands of feet below the ocean surface, allowing for efficient extraction of oil and gas.
Artificial Lift Systems: In wells where natural flow is insufficient, ESP cables power electric submersible pumps as part of artificial lift systems. These systems are crucial for maintaining or enhancing production rates, especially in mature or low-pressure reservoirs.
High-Temperature & High-Pressure Wells: ESP cables are engineered to withstand extreme downhole conditions, including high temperatures and pressures. They enable the operation of electric submersible pumps in wells with challenging geothermal gradients or formations containing high-pressure fluids.
Corrosive Environments: With specialized insulation materials like high-dielectric EPDM rubber and corrosion-resistant armor options like MONEL alloy, ESP cables are well-suited for use in wells containing corrosive gases, acids, or other aggressive fluids. This ensures reliable operation and extended service life even in harsh environments.
Chemical Injection Systems: ESP cables often incorporate stainless steel capillary tubes for the injection of scale and corrosion inhibitors. This helps maintain the integrity of the wellbore and production equipment, minimizing downtime and maximizing production efficiency.
Remote Monitoring & Control: In addition to powering the electric submersible pump, ESP cables can also be used to transmit data from downhole sensors to the surface. This allows for real-time monitoring of well conditions, enabling operators to make informed decisions and adjust production parameters as needed.
Horizontal & Deviated Wells: ESP cables are flexible enough to be deployed in horizontal and deviated wells, which are becoming increasingly common in modern oil and gas exploration and production. Their ability to withstand the bending and torsional forces associated with these well types ensures reliable power transmission and pump operation.
ESP cables play a vital role in enabling efficient and cost-effective oil and gas production in a wide range of challenging subsurface environments. Their unique design and materials make them indispensable for deepwater drilling, artificial lift systems, high-temperature/high-pressure wells, corrosive environments, and more.
ESP Cable Manufacturer and Price
Dosense Cable, ESP Cable factory, ESP Cable Supplier, We offer high-quality cabling solutions at incredibly low prices. Our manufacturing expertise ensures long-lasting and reliable cables, perfect for electrical and infrastructure projects. Contact us and find out why our cables are the best investment for your project.